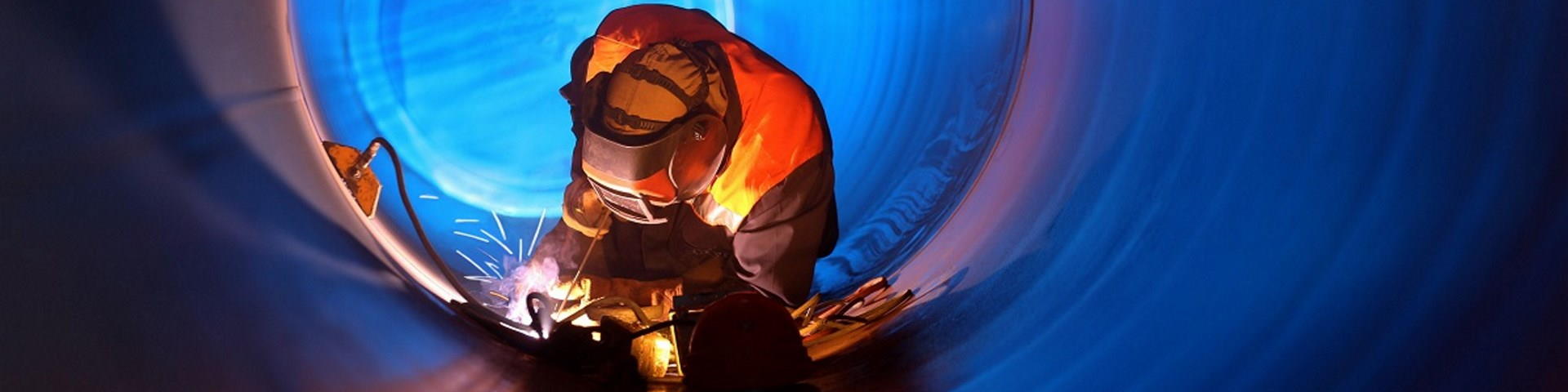
Процесс экзотермической резки основан на горении специального стержня-электрода в кислородной струе низкого давления. В отличие от других процессов резки, экзотермическая резка позволяет разрезать, производить строжку и прошивку отверстий на различных материалах (сталях, сплавах цветных металлов, чугуна, бетона, огнеупорных материалах, камня и т.д.). Процесс имеет очень высокую производительность и прост в применении.
ПРЕИМУЩЕСТВА
- универсальность
- высокая скорость реза
- удобство и простота в использовании
- не требуется предварительный нагрев
- автономность (не требуется силовая электрсеть)
ОСОБЕННОСТИ
Позволяет резать труднообрабатываемые материалы:
- н/у стали;
- нержавеющие стали;
- низко м высоколегированные стали;
- чугун;
- алюминиевые сплавы;
- магниевые сплавы;
- цветные металлы;
- шлак и огнеупорные материалы;
- бетон и камень.
ПРИМЕР РЕЗАКА ДЛЯ ЭКЗОТЕРМИЧЕСКОЙ РЕЗКИ
РУКОВОДСВО ПО ВЫПОЛНЕНИЮ ЭКЗОТЕРМИЧЕСКОЙ РЕЗКИ
Стандартная резка.
Подайте кислород в резак и зажгите стержень-электрод с помощью внешнего источника питания. Начните резку. Стандартная резка выполняется методом опирания. После контакта электрода с заготовкой, нужно, не отрывая электрода, вести его в направлении реза. Если при этом вы не видите разрез, то скорость резки нужно уменьшить. Если электрод расходуется слишком быстро, то скорость резки нужно увеличить. Следите за подачей кислорода, без него процесс резки остановится. Если заготовка имеет толщину более 50мм, то используйте распиливающие движения, чтобы обеспечить разрез на всю толщину заготовки. При завершении резки распиливающие движения надо сделать более плавными, это улучшит внешний вид разреза. При работе в стесненных условиях старайтесь не задеть находящиеся поблизости предметы и материалы. Для завершения резки отключите подачу кислорода, и процесс, через некоторое время, завершится. После завершения процесса резки, держите резак на безопасном от себя расстоянии, пока не остынет электрод.
Прожог (прошивка) отверстий
Для получения отверстий в материале используется тот же резак, что и для стандартной экзотермической резки, только в комплекте с удлинителем цанги и защиты. Удлинители продлевают срок службы резака, и обеспечиваю комфорт оператора (резчика). При прошивке старайтесь держать резак на расстоянии вытянутой руки и используйте средства защиты глаз, органов слуха и тела. По мере прожигания отверстия, медленно вращайте стержень из стороны в сторону, чтобы избежать неравномерного выгорания стержня электрода по сторонам. После прошивки отверстия извлеките стержень электрода из полученного отверстия и отключите подачу кислорода. Если подачу кислорода прекратить во время прошивки, стержень электрода может застрять, поэтому этого делать не стоит. Ниже приведен порядок действий при прошивке отверстий.
- Зажгите стержень электрода.
- Расположите резак на расстоянии вытянутой руки, так чтобы стержень электроды был перпендикулярен заготовке.
- Медленно вдавливайте стержень в заготовку, до тех пор, пока не достигните нужной глубины реза или полностью не прошьете заготовку.
- Извлеките стержень электрода из прошитого отверстия и после этого отключите подачу кислорода.
Процесс прожога (прошивки) отверстий также используется для резки бетона. Прошив несколько отверстий в бетоне, его становиться гораздо легче разломить. Это существенно экономит время по сравнению с обычной механической резкой бетона.
Расход кислорода
В процессе резки можно использовать кислород промышленной чистоты. Рекомендуемое давление кислорода для данного процесса 0,55МПа. Если толщина заготовки более 75мм, то давление кислорода можно увеличить. Низкое давление 0,27МПа используется для срезания заклепочных головой или разделки мелких трещин.
Расход кислорода для стержней электродов д.6,4мм составляет 198 – 212 л/мин, а для д.9,5мм – 311 – 339л/мин. Данные значения могут корректироваться в зависимости от процедуры.
Время горения стержней электродов
В зависимости от вида материала, его толщины и нужной скорости реза выбирается электрод нужного размера (см.табл.).
Разрезаемый материал |
Толщина, см |
Электрод, см |
Скорость резки, см/мин. |
---|---|---|---|
Углеродистая сталь |
0,318 |
5,7 |
183 |
0,635 |
3,8 |
132 |
|
0953 |
3,5 |
106 |
|
1,27 |
3,2 |
89 |
|
1,91 |
1,9 |
56 |
|
Нержавеющая сталь |
0,318 |
5,1 |
165 |
0,635 |
2,9 |
91 |
|
Алюминий |
0,635 |
4,4 |
147 |
0,953 |
3,2 |
97 |
|
1,91 |
1,9 |
58 |
Данные таблицы получены экспериментальным путем и могут отличаться от фактических значений.